Vessel motion – MySep and CFD compared
Sea surface motion subjects the entirety of a Floating Production Storage and Offloading (FPSO) facility to movement and acceleration forces. This in turn imparts motion to the fluids inside separation vessels. A designer needs to ensure that separation internals and vessel nozzles are suitably located and dimensioned to avoid control or separation performance issues.
Summary
- New module in MySep v3.0 calculates liquid levels for vessels subjected to motion
- Rapid design and evaluation for fast track projects
- Excellent agreement with general trends in CFD predictions
- Greatly reduces scope of CFD simulations recommended for final evaluation
- Major reductions in engineering cost and project time
Screen Designs to Avoid
- Partial submergence of the inlet device resulting in excessive re-entrainment (carryover)
- Liquid level reaching the bottom of a demisting device resulting in syphoning through the drain pipe and consequent excessive carryover
- Liquid outlet nozzles becoming exposed to gas with consequent gas flow penetrating the liquid handling system
- Level control issues due to the liquid level exceeding the instrumentation range
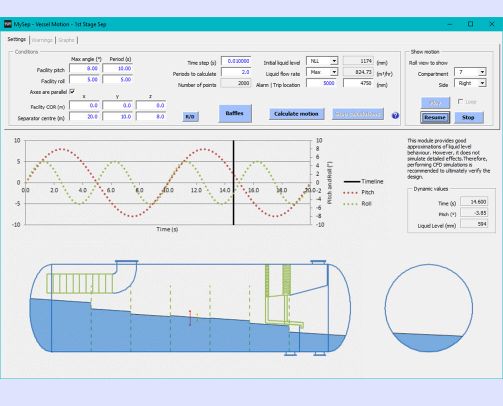
MySep Motion Modelling
In MySep v3.0 the Motion module was introduced to mitigate the con’s of the trigonometry and CFD approaches to liquid motion modelling, whilst retaining their pro’s as much as possible. The new capability provides the process engineer with a means to rapidly
analyse liquid motion in a separation vessel with reliable results in minutes rather than days/weeks.
The calculations that resolve the liquid level behaviour are based on the physics of fluid dynamics. As the vessel is subjected to motion (pitch and roll), the liquid in the separator is subjected to a number of forces, in addition to gravity. These forces are dependent on the pitch and roll angels and periods, as well as on the location of the separator relative to the centre of rotation of the floating facility. While these accelerations induce the flow of liquid, perforated anti-sloshing baffles in the vessel provide a restriction of flow.