Digital Twin Tackles LNG Separation Challenge
Against a backdrop of increasing demand for LNG, continued investment in new liquefaction plants and the drive to optimize existing plant profitability, the demonstrated value of a process digital twin has never been more important.
This use case features the SLB (Schlumberger) Symmetry simulation platform, MySep Engine rigorous separator models and additionally, MySep Studio for exploration of separator retrofit options.
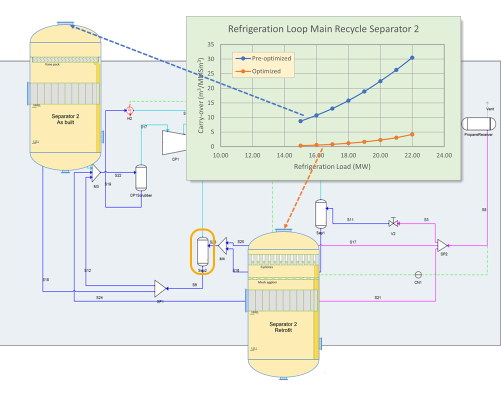
Digital Twin Analysis 1
The digital twin reveals that as more gas is processed and condensed, to produce LNG, the refrigeration load must increase. This is achieved by increasing the recirculation of refrigerant. The higher vapor flow leads to significant carry-over in certain separators. The graph here shows a blue curve representing carry-over from the main IP recirculation separator, designated Sep 2 on the Symmetry PFD. Whilst there is no specific limit defined for permissible carry-over in this unit, it feeds the IP Suction Separator, CP2.
The effect of updating our digital twin, with a potential retrofit to Sep 2, is shown in the lower orange carry-over curve. We can see carry over from Sep 2 can be reduced considerably across a range of refrigeration loads corresponding to higher LNG production.
Digital Twin Analysis 2
Further analysis with our digital twin, modelling the as-built separator arrangements, reveals a small but significant carry-over of liquid from the CP2 Scrubber. This separator, upstream of the suction of the intermediate stage (IP) compressor is fed by vapour from three sources: the cold-side outlet of the main liquefaction exchanger; vapour from the discharge of the 1st stage compressor and vapour with liquid carry-over from the main IP recirculation separator.
Without optimizing any of the system separators, the blue plot shows that a modest increase in production, will quickly result in carry-over beyond the specified mist loading limit (red line) for the IP Suction Separator.
We can explore the potential to retro-fit any of the refrigeration loop separators with up-graded
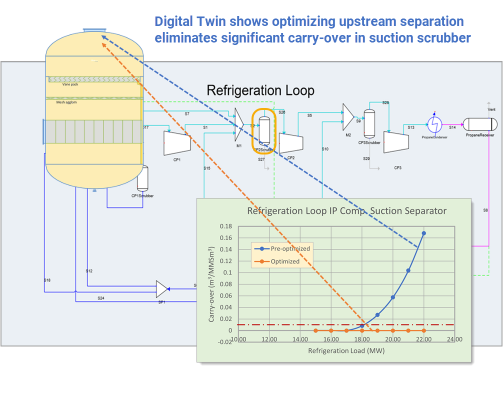
Challenge
Optimization of an LNG process to maximize production demands recognition of the physical constraints represented in process separators. This study focuses on constraints in the refrigeration loop which provides cooling for the main liquefaction process. Excessive liquid carry-over with vapour flow in compressor inlet separators, (suction scrubbers) is potentially damaging to the compressor. It is usual to impose liquid carry-over limits to maintain asset integrity and avoid un-planned shut-down. These limits result in constraint to system cooling capacity, resulting in the restriction of capacity of the entire process, limiting LNG production, plant revenue, and profit.
Solution
MySep Engine models were included in a process digital twin, constructed in the SLB Symmetry process simulator. The model allowed analysis of the impact of increased refrigeration demand, which in turn requires increased refrigerant circulation rate. Embedding MySep incremental analysis of gas-liquid separation for defined separator geometries, yields a physically accurate representation of carry-over in the system separators. This is easily achieved with the MySep Engine software module embedded in the Symmetry Digital Twin. The combined digital twin allows the process optimization team to understand which separators might exceed operational carry-over limits. Studies can readily be undertaken to explore how the system will behave with increasing production throughput.
Results
MySep Studio software allows careful exploration of options to retro-fit the existing process separator vessels, with up-graded internal devices. These can then be incorporated in the MySep Engine individual separator models. The updated digital twin can demonstrate increased refrigeration and processing capacity, with the assurance that MySep’s accepted modelling methodology brings. Up-graded separators in the digital twin demonstrate production capacity can considerably increase, without unacceptable levels of liquid entrainment in compressor suction.
Conclusions and More Information
In this study it was demonstrated that a modest investment of $500k - $700k could increase the plant refrigeration capacity of a single train, by around 20MW. This in turn could support a 15% increase in LNG production.
A more complete description of the case study featured here, can be found in the MySep’s article, published in the March 2023 issue of LNG Industry journal.
For more information on how MySep can help operators and designers of LNG processes.